structural Industrial Building
Forging Tomorrow's Foundations Today
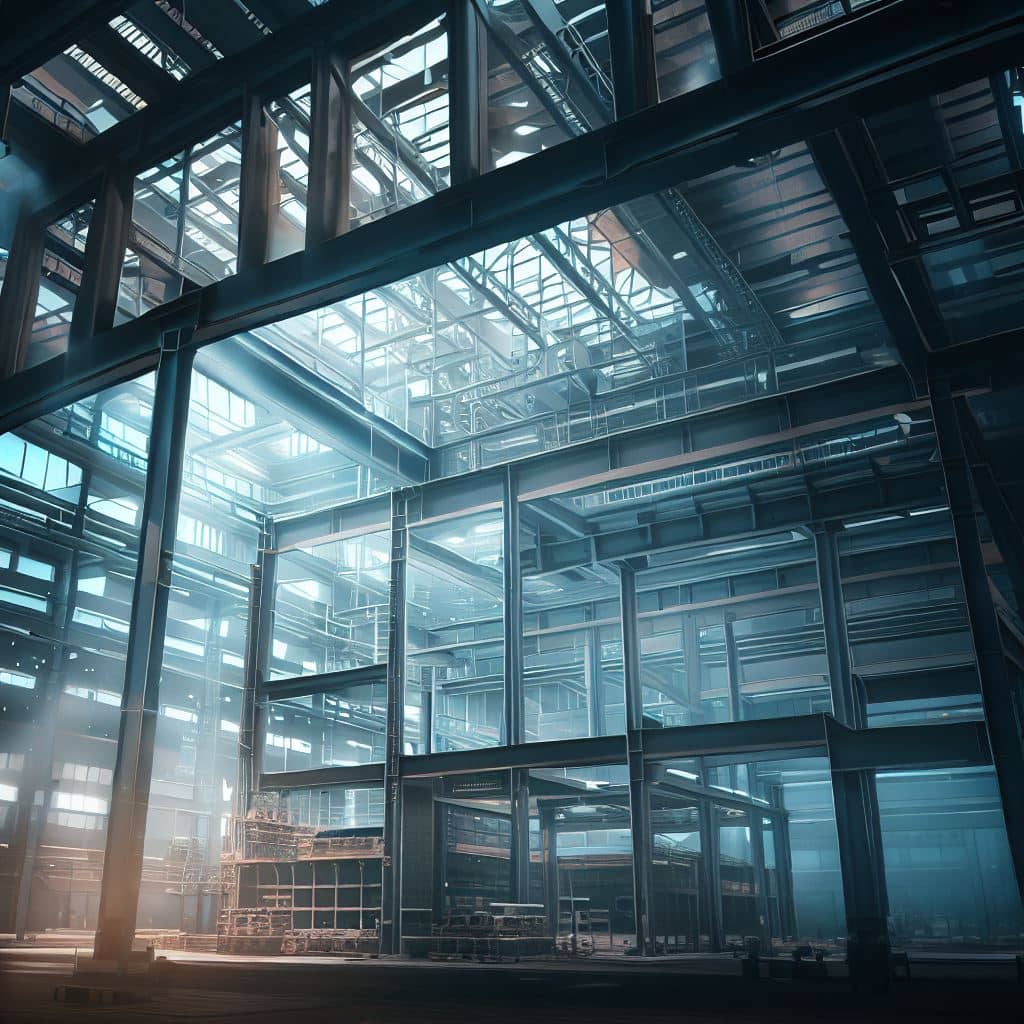
Welcome to Vinayak Steel Profiles' Steel Structural Industrial Building Solutions, where we merge innovation and reliability to shape industrial spaces that redefine productivity, efficiency, and safety. Our comprehensive services span the entire spectrum of industrial construction, from inception to the final beam placement. We understand that industrial facilities are the backbone of countless industries, and our commitment is to provide tailored solutions that exceed expectations.
Design Excellence:
Precision Fabrication:
Efficient Project Mastery:
Safety and Sustainability:
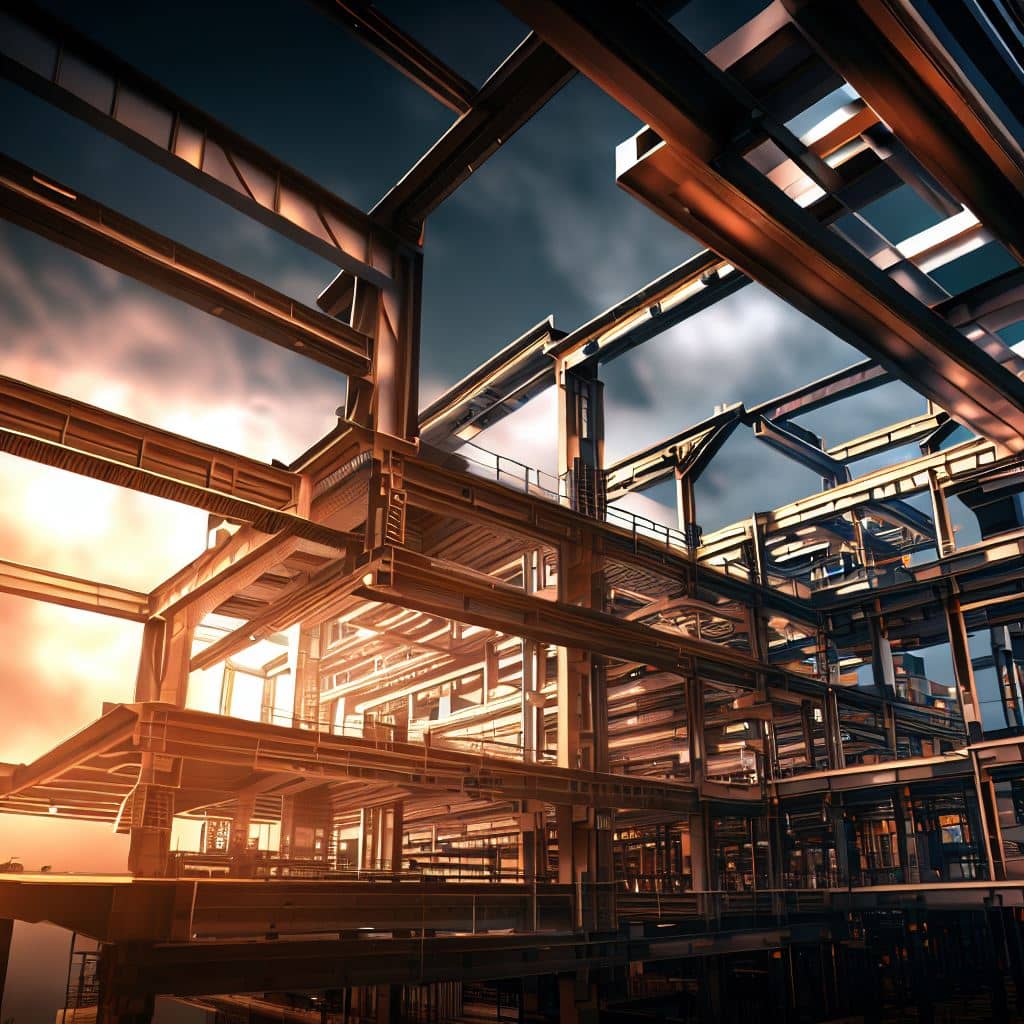
The process for steel structural industrial building typically involves several key steps, each critical for ensuring the successful completion of the project. Here's an overview of the typical process:
1. Project Initiation and Planning:
Needs Assessment: The process begins with a thorough assessment of the client’s needs and requirements. This includes understanding the purpose of the industrial building, size specifications, layout preferences, and any unique features needed.
Site Selection: If the site is not already chosen, the client and the construction team work together to select the optimal location for the industrial building, considering factors like accessibility, utilities, and zoning regulations.
Budget and Timeline: A budget and project timeline are established, outlining the financial scope and expected duration of the project. This step is crucial for financial planning and resource allocation.
2. Design and Engineering:
Conceptual Design: Architects and engineers work collaboratively to create a conceptual design that aligns with the client’s vision. This phase focuses on layout, functionality, and overall aesthetics.
Detailed Design: Once the conceptual design is approved, it is refined into detailed architectural and engineering plans. These plans include structural calculations, material specifications, and precise blueprints.
3. Permits and Approvals:
- Regulatory Compliance: The project team navigates the permitting process, ensuring that the design and construction plans comply with local building codes and regulations. This often involves submitting plans to local authorities for review and approval.
4. Fabrication:
Materials Procurement: After approvals are obtained, materials such as steel beams, columns, roofing, and other components are sourced from trusted suppliers. Quality control measures are in place to ensure materials meet required standards.
Fabrication: Structural components are fabricated according to the detailed engineering plans. This process takes place in specialized workshops equipped with advanced machinery for precision cutting and welding.
5. On-Site Construction:
Site Preparation: The construction site is prepared, which may involve grading, excavation, and foundation work.
Erection: Steel structural components are transported to the site and assembled according to the detailed engineering plans. This phase includes the installation of columns, beams, walls, roofing, and any other required elements.
Utilities and Services: Electrical, plumbing, HVAC, and other utilities are installed as needed.
6. Quality Control and Safety:
Quality Assurance: Throughout the construction process, quality control checks are performed to ensure that the work meets industry standards and adheres to the approved plans.
Safety Measures: A strict focus on safety is maintained throughout the construction. Safety protocols are enforced to protect workers and ensure compliance with safety regulations.
7. Interior Build-Out (If Applicable):
- If the industrial building requires interior construction, this phase includes the installation of walls, flooring, lighting, and other interior elements.
8. Final Inspections and Testing:
- Before the building can be occupied or used for its intended purpose, final inspections are conducted to ensure that all construction work meets regulatory standards.
9. Handover and Occupancy:
- Once all inspections are passed, the project is handed over to the client. This includes the turnover of keys, relevant documents, and warranties for the building and its components.
10. Post-Construction Services:
- The construction team often provides post-construction services, such as maintenance and support, to address any issues that may arise after occupancy.
This comprehensive process ensures that steel structural industrial buildings are designed, fabricated, and constructed efficiently, meeting safety and quality standards while fulfilling the client’s needs and vision.